Electric welding machines operate on the principle of using electrical current to generate heat, melting metal pieces and fusing them together. This process allows for the creation of strong and durable welds, essential in industries ranging from automotive manufacturing to infrastructure development and even intricate metal artistry.
One of the key advancements in electric welding machines is the variety of welding techniques they offer. From Shielded Metal Arc Welding (SMAW) and Gas Metal Arc Welding (GMAW) to Flux-Cored Arc Welding (FCAW) and Tungsten Inert Gas Welding (TIG), these machines cater to diverse welding needs across different materials and applications. Each technique provides specific advantages in terms of weld quality, speed, and suitability for different metals and thicknesses.
Electric welding machines also encompass versatility in their adaptability to various welding positions and environments. Whether it's flat, horizontal, vertical, or overhead welding, these machines offer flexibility and control, enabling welders to work in diverse settings and orientations. Additionally, advancements in portable and compact welding machines have expanded their usability in remote locations or confined spaces, providing convenience and accessibility.
the precision and control offered by electric welding machines contribute to superior weld quality. Adjustable parameters such as current, voltage, and wire feed speed enable welders to fine-tune their welds, ensuring uniformity, strength, and minimized defects. This level of control allows for intricate welding tasks, from delicate automotive welding to heavy structural fabrication, with consistent and reliable results.
The evolution of electric welding machines also incorporates technological innovations that enhance efficiency and safety. Automated features such as digital interfaces, pre-set welding programs, and sensors for monitoring welding parameters optimize the welding process, reducing human error and improving productivity. Additionally, safety mechanisms, including overload protection and arc force control, prioritize user safety, minimizing risks associated with welding operations.
Electric welding machines have also played a crucial role in environmental sustainability. Efforts to improve energy efficiency and reduce emissions have led to the development of eco-friendly welding technologies, making these machines more environmentally conscious. Additionally, advancements in welding consumables and materials aim to minimize waste and enhance recyclability, contributing to greener practices in metalworking industries.
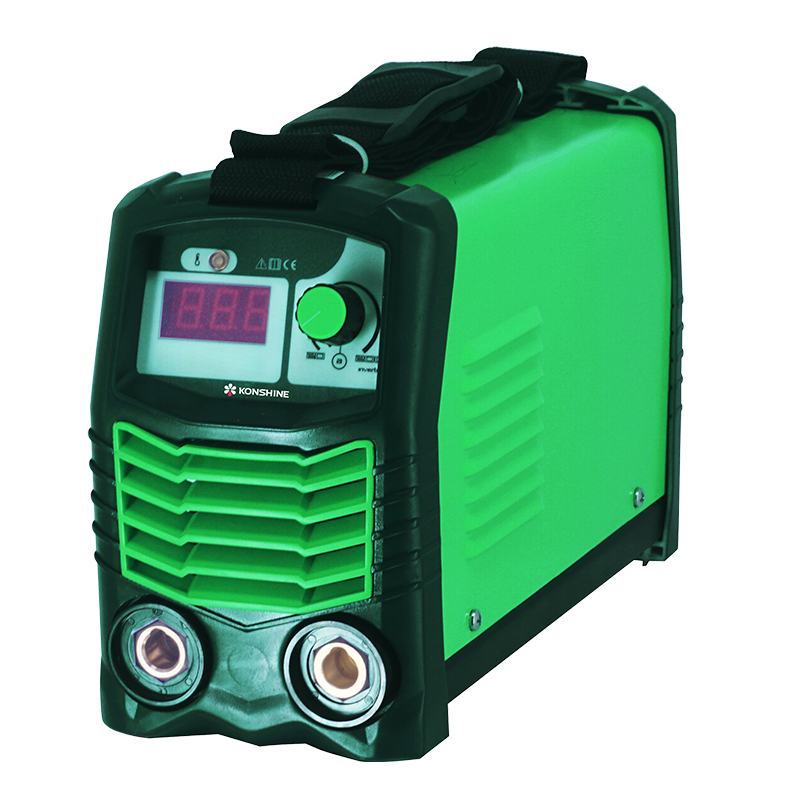